Méthodes de diagnostic prédictif sur machines tournantes
Diagnostic et analyse Linkeo / 30 Avril 2025
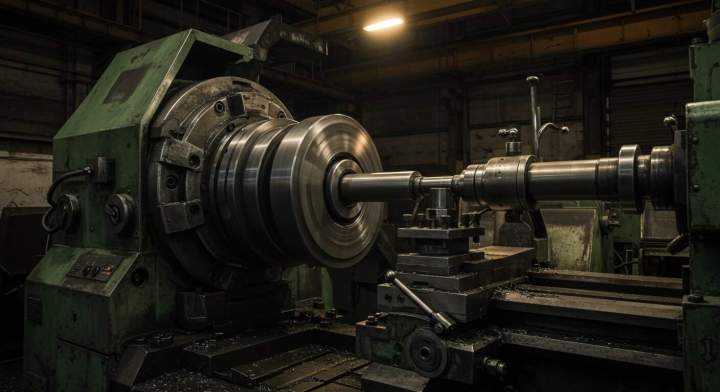
Méthodes de diagnostic prédictif sur machines tournantes
Qu'est-ce que le diagnostic prédictif ?
Le diagnostic prédictif est une technique de maintenance qui utilise des données et des analyses pour prédire les défaillances potentielles des machines. Contrairement à la maintenance préventive, qui repose sur des intervalles fixes de maintenance, le diagnostic prédictif se base sur l'état réel des machines. Cela permet d'intervenir uniquement lorsque cela est nécessaire, réduisant ainsi les coûts et les temps d'arrêt.
Les principales méthodes de diagnostic prédictif
1. Analyse des vibrations
L'analyse des vibrations est l'une des méthodes les plus courantes pour le diagnostic prédictif. Elle consiste à mesurer les vibrations émises par une machine en fonctionnement. Les anomalies dans les motifs de vibration peuvent indiquer divers problèmes, tels que :
- Désalignement
- Balourd
- Usure des roulements
Avantages
- Détection précoce des pannes
- Évaluation non intrusive
- Amélioration de la durée de vie des équipements
2. Thermographie infrarouge
La thermographie infrarouge utilise des caméras thermiques pour détecter les variations de température sur les surfaces des machines. Des points chauds peuvent signaler des problèmes électriques ou mécaniques. Cette méthode est particulièrement utile pour identifier :
- Surchauffe des moteurs
- Mauvais contacts électriques
- Fuites thermiques
Avantages
- Analyse rapide et précise
- Identification des problèmes avant qu'ils ne deviennent critiques
- Aucune interruption du fonctionnement de la machine
3. Analyse d'huile
L'analyse d'huile consiste à examiner les propriétés de lubrifiant dans les machines. Des contaminants, tels que des particules métalliques ou des additifs dégradés, peuvent indiquer une usure excessive ou une défaillance imminente. Les principaux tests incluent :
- Spectrométrie
- Analyse de viscosité
- Tests de contaminants
Avantages
- Fournit des informations sur l'état interne de la machine
- Permet de planifier des interventions en fonction des résultats
- Réduit les risques de défaillance catastrophique
Technologies associées au diagnostic prédictif
1. Internet des objets (IoT)
L'IoT joue un rôle crucial dans le diagnostic prédictif. En connectant des capteurs sur les machines, il est possible de collecter des données en temps réel. Ces données peuvent ensuite être analysées pour prévoir des défaillances.
2. Intelligence artificielle (IA)
L'IA et l'apprentissage automatique permettent d'analyser de grandes quantités de données pour identifier des modèles et des anomalies. Ces technologies améliorent la précision des prédictions et aident à prendre des décisions éclairées.
3. Systèmes de gestion de la maintenance assistée par ordinateur (GMAO)
Les GMAO intègrent des outils de diagnostic prédictif, facilitant la planification et le suivi des interventions. Cela permet une gestion optimisée des ressources et un meilleur contrôle des coûts.
Conclusion
Le diagnostic prédictif sur machines tournantes est une approche essentielle pour les industries modernes. En intégrant des méthodes telles que l'analyse des vibrations, la thermographie infrarouge et l'analyse d'huile, les entreprises peuvent anticiper les défaillances et optimiser leur maintenance. L'émergence de technologies telles que l'IoT et l'IA renforce encore cette capacité, permettant une gestion proactive et efficace des ressources. Adopter ces méthodes est un investissement judicieux pour toute organisation cherchant à améliorer sa productivité et sa rentabilité.